RECENTLY VISITED
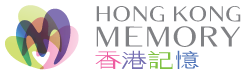
Industry Focus
The origins and development of garment industry in Hong Kong
The term “Garment manufacturing” comprises two levels of meanings. It is a process and also an industry. Spinning, weaving, dyeing and sewing are four necessary processes in manufacturing garments. In the early years, the raw materials of garments were cotton textile, therefore “sewing” or “garment manufacturing” was the last process of the cotton-related industry. Many of the large yarn factories in Hong Kong were operated using the “one-stop” production model and garment manufacturing was one of the large departments; at the same time, many garment manufacturing factories did not deal with spinning, weaving or dyeing. They had to rely on local and overseas spinning factories to provide them with knitted fabric. Therefore, garment manufacturing can be regarded as an independent industry. The post-war official industrial statistics addressed the textile industry and the garment industry as two separate entities.
Garment factories can be categorized by products: top (shirt), bottom (trousers), suit, thick and thin garment. Each piece was manufactured in different departments in large-quantity and each worker was responsible for a particular process. The post-war garment factories in Hong Kong were mainly owned by businessmen from Guangdong. Many tailors from Shanghai and Chiuchow also started home-based workshops. Exquisite handicraft like drawnwork, embroidery and Gu embroidery was their selling point, and they offered tailor-made, up-market clothing. Buttons, zippers and printing were peripheral industries attached to garment industry. When talking about Hong Kong garment industry, we refer mainly to garment factories with a flow line production.
The garment industry in Hong Kong took shape in the early twentieth century. At that time there were no independent “garment factories”. The garment department was one of the departments of a weaving mill. Apart from supplying fabrics, many weaving mills produced garments through simple procedures. Factories dedicated to garment manufacturing, and that took names with such words as “Clothing” or “Garment” appeared in the early thirties. Kwong Hing Tai Company, Kwok Man Underwear Company, Kwok Hing Garment Co.,Ltd were some of the large factories found before WWII. Before the war, clothing produced in Hong Kong comprised mainly middle-priced to low-priced products such as vests, cotton knitwear, cotton stretch tee, briefs, cotton-knitted socks, swimsuit etc. They were exported to the Mainland, Nanyang, the Britain Commonwealth and British colonies.
Western clothing became popular around the world after the war. Many Chinese gradually changed their habits and switched from tailor-made Chinese-style clothing to western style shirts and trousers which became a trend. Also, at the end of 1940s many refugees came to Hong Kong and they brought in a large amount of cash, technique and cheap labour, contributing to the prosperity of the garment industry. Post-war garment industry can be briefly classified into four stages: I) Era of exporting to British Colonies (post-war to 1950s); II) Era of exporting to Europe and America (from the end of 1950s); III) Era of setting up factories in poor countries in Asia (from early 1970s); IV) Era of setting up factories in mainland China (from early 1980s). 1970s and 1980s were the golden ages of garment industry. Among all other manufacturing industries, it was the leading industry in terms of number of factories, number of employees and total export value.
The change in product variety and materials
Local garment factories mainly produced underwear before the war. Among them, cotton knitwear, cotton stretch tee and cotton socks were the most popular. In the years right after the war, garment factories produced mainly shirts. In the eye of the general public, garment factories were shirt factories. Shirts made in Hong Kong were mainly mass produced and of mid-to-low pricing. Apart from supplying locally and to the mainland, shirts were also exported to the British colonies such as Malaysia, East Indies, India and Ceylon etc.
Towards the end of 1950s, the opening of the Europe and America market brought the price up for garments exported from Hong Kong, and the variety were more diversified and expanded to trousers, jackets, sleepwear, sportswear etc. Since 1961, the total export value of outfit and trousers had surpassed that of shirts. In the early 1970s, jeans swept through the European and American continents and many local garment factories put them into production. Jeans became the garment with the highest value of total exports of the year. In 1980s, many big garment factories developed their own brands and strengthened the bond between their products with the trend to launch mid-to-high end fashion.
Regarding the methods of knitting the materials, as woven fabric had a longer history, and was produced extensively, it was more suitable for the mass production of mid-to-low price garments. Woven fabrics thus became the mainstream after the war till 1960s. Main garment factories using woven fabrics were Lai Sun Garment, Yangtzekiang Garment and Esquel Garment. Since 1960s, knitted garments became popular. As knitted fabrics could be produced in small-scale and in more styles, its sportswear and casual wear were welcomed by the public. Main knitted garment factories included Laws Garment and Knitting, Fong’s, Unison Knitting and Zentes. Wool knitting is a stream of knitting which flourished in the 1980s and 1990s. Accessories such as shawls were favoured by fashion consumers. Laws Garment and Knitting was an exemplar of the industry this stream.
Before 1960, local garment factories used fabrics mainly from overseas. About seventy per cent of the export garments were processed from imported fabrics; with the prosperity of local textile industry, over fifty percent of the fabrics for export garments were supplied by local factories in the middle of 1970s, especially for denim, khaki and corduroy. Garment factories using local fabrics could lower production costs and raise its competitiveness towards nearby regions.
Production Models: OEM and brand development
Local garment owners had always relied on foreign companies to get in touch with the overseas market. The reason was because they were not familiar with foreign legal systems and culture. Also, the communication channels were not developed. Most garment factories sold their products to foreign companies and these companies directly traded with overseas customers. For example, Dodwell & Co. Ltd. ran business for the British market, and C. Melchers GmbH & Co for the German market, foreign companies owned by Indians operated business for markets from India to African. Garment factories with better finances had another way out. Starting from the end of 1950s, they set up offices in Europe and America, hired local salesmen or cooperated with local agencies so as to get in touch with traditional fashion brands to build the OEM production model.
Since 1960s, OEM had been the core business model of garment industry. American chain-stores like Wal-Mart and K-Mart ordered low-cost garments from Hong Kong garment factories. Local garment factories also produced garments designed by Europe and American brands and supplied them with finished products. For example, Yangtzekiang Garment produced fashion for such brands as Marks & Spencer, Hugo Boss, Marc Jacobs, Nike and Littlewood etc. Such OEM orders were usually stable and large so they were the lifeblood of garment factories; big factories might subcontract part of the order to some middle or small sized factories so as to meet the deadline. These middle or small factories might further split the order to some small-scale factories or even home-style workshops which formed the layers of a sub-contracting web. Such sub-contracting could be by piece, or by a particular process.
Soon after the war Hong Kong garments were exported to the British colonies. Large textile companies and garment factories set up sales department in the Southeast Asia, exported and sold goods directly there. Exported shirts produced in Hong Kong had built their brand in the early years, for example, “The Eagles” by “Kwong Hing Tai” and “The Professor” by Yangtzekiang Garment. However, such catchy brands served only to impress customers and the quality could not be compared to the European and American brands which distinguished themselves by unique designs.
The profit of selling was higher than producing garments. Since 1970s, some garment factory owners started up sales department and some big garment factories started to develop their own brands. They took reference from overseas fashion brands as they created their own brands. For example, Yangtzekiang Garment developed their own brand “Michel Rene” with a French take on the style. They produced and marketed their products. Apart from developing their own brands, garment factory owners also invested in representing certain brands. They brought famous brands from Europe and America, or produced and marketed the brands by themselves, or they collected commission from the retailers. For example, Novel Group had acquired famous U.S. fashion brand Tommy Hilfiger and Chao’s family, founder of the Novel Group, became Hong Kong’s business representative to develop business in the U.S. Apart from promoting foreign brand, there were local garment factories running chain stores for their brands. For example, Bossini was a local brand selling leisurewear in chain stores established in 1987 by the founder of the Laws Group Law Ting Bong.
International market and quota system
Hong Kong’s garment industry has always been directed by export. Before the 1960s, the export market focused on developing countries in which local textile industry was weak. At the same time, Hong Kong was a British colony so it enjoyed the benefits of the preferential tariff treatment offered by countries of the British Commonwealth. It enjoyed privileges when exporting garments to the United Kingdom and the United Kingdom had become one of the main markets for Hong Kong garments; From 1960s, Hong Kong garments were also massively imported to the U.S. market. But since 1950s, many European and American countries had gradually set up trade protection measures to protect their own garment industries. For example, in 1959 Hong Kong had signed an agreement with the United Kingdom to voluntarily restrict the export quantity of cotton textiles; in the International Cotton Textile Meeting held in Geneva in July 1961, a “short-term arrangement” was set on international cotton textile trade to restrict the exporting quantity of twenty-two kinds of Hong Kong textile products. In the early 1970s, the U.S. had officially assigned quotas to Hong Kong cotton textile products and the restriction had later extended from cotton to polyester fibers and chemical fibers.
In 1970s, various kinds of garment products – pure cotton, mix cotton and synthetic fibers etc. were developed. From 1974, Hong Kong had officially named the earlier bilateral trade agreement set with EU and the U.S. as “Multi-fiber Agreement”. The agreement had systematically assigned codes to various textiles and the restriction was initially for cotton, synthetic fibers and wool, but in 1986 it had extended to ninety percent of textile products exported to the U.S. The agreement explained how the quota system should be implemented: the importing and exporting counties may negotiate quota restrictions based on recent exporting situation and set the exporting quantity and variety, then with reference to the quantity of garment production in various factories quotas were assigned.
Garment industry was the biggest industry in Hong Kong. The Hong Kong Government had great concerns about how the quota had influenced the industry. In 1970s and 1980s, it sent various delegations to participate in international trade conferences and negotiated with EU and the U.S. on the quota issue of textile products. This series of quota negotiations on textile products were governed under the “General Agreement on Tariff and Trade” (GATT) conference organizations. Hong Kong government sent the Deputy Director of Trade and Industry Department as chief representative of negotiation, and Textile Advisory Board (TAB) members attended so as to give immediate advice. TAB members were appointed by the government and were from the industrial sector and the business sector. The Hong Kong delegation played a leading role among the Asian countries. In those years, many Hong Kong businessmen set up factories in Southeast Asia and they were active in their local textile industries. They also participated as representatives of those countries and negotiated on the quota in the meetings. In those international meetings, members from Hong Kong garment industry represented different countries to negotiate on quota restrictions.
All these quotas and product origin restrictions had profound influences on the garment industry. Quotas were assigned according to the quantity of production so large factories or factories with a long history hold more quotas. Some factories resold the quotas to factories with no or insufficient quotas to obtain profits; small factories with no quotas could only took over the outsourced orders from big factories and relied on big factories to survive; some factories rearranged their production, such as raised the quantity of high priced garments and the products unrestricted to export. Many big factories built factories in countries unrestricted by the quotas. Closer ones were Macau and Taiwan, and further ones were Southeast Asia, South Asia and Africa, and directly from there they exported the products to developed countries like Europe and the U.S.
As Hong Kong was a British colony, many Hong Kong businessmen took British colonies as their first choice for investment. Singapore, Malaysia, Myanmar, Sri Lanka and Bangladesh were top choices. They obtained overseas investment information mainly through organizations like the Hong Kong Trade Development Council, British banks and KPMG etc. To set up factories in less developed countries, Hong Kong businessmen enjoyed the benefits of cheap land and labour, and in turn supported the local textile industry so it was welcome by the local governments. Of course they had to tackle operational problems brought by cultural differences.
Factories, workers and production techniques
Before the war, cotton textile factories dominated the garment industry and were located in districts such as Sham Shui Po, Mongkok, Yau Ma Tei and Kowloon City etc; there were a few garment factories scattered in Central & Western District and Kowloon City. In the early years after the war, garment industry prospered and factories mainly gathered in Sham Shui Po and Cheung Sha Wan. There were many factories producing textiles and clothes around so the supply of raw materials was abundant. A “through-train” interactive relationship was formed among the factories. Big companies usually built one whole building as their factory, smaller ones rented a floor. There were also even smaller informal or home-style workshop scattered around Hong Kong. In the early 1960s, the Hong Kong government developed industrial districts like Kwun Tong and San Po Kong. As the land use was restricted as industrial the price was cheaper so it attracted many factory owners to buy the land and build the factories; at the same time the government built industrial buildings and rented them to smaller factories. The government also built resettlement buildings next to them so as to provide labour to the factory owners.
Garment industry was labour-intensive. The garment factories were of smaller scale before the war. A factory with dozens of workers would be regarded as big. The industry developed rapidly thirty years after the war. Workers in the garment industry accounted for fifteen percent of labour during the peak. Big factories could easily employ thousands of workers. The larger the garment factory, the more sophisticated the division of labour in production. Division of labour was assigned according to types of garments and processes of sewing. The more sophisticated the division, the lower the skills required. The division is less sophisticated in smaller factories yet the skills required were higher.
The male and female ratio in garment industry was about thirty to seventy. There was a clear gender division of labour. Male were usually skilled workers or technicians and they monopolized cutting and ironing. Female were usually manual or unskilled workers mainly responsible for sewing and packing etc. After working in big factories for a few years, some masters of cutting started up small or informal factories to take outsourced orders from their former employees or from other big factories. Factory workers were usually paid by piece so it helped to raise motivation while at the same time lower the factory’s production costs.
In the 1970s and 1980s, the industry was booming to such scales that manufacturers were too busy to attend to all orders during the peak seasons. They outsourced their orders to informal or home-style workshops. During those years, many married women who had worked in factories started up sewing workshops at home, or rented a place at resettlement buildings or at the public housing so as to take orders from big factories. The outsourced work helped these women balance work and family. At the same time, it allowed manufacturers to retain a flexible production team. Home-based workers with better craftsmanship could be assigned to make samples and earned more per piece.
Swift to the north and restructuring of the industry
In the early 1980s, Hong Kong’s land and wages were raising rapidly. Like other labour-intensive industry such as watches, toys and electronics, garment industry faced pressure from the increasing operational costs. The opening and reform allowed China to actively introduce investments from over the border and encourage Hong Kong businessmen to set up factories there. Privileges on tax and land price were offered; in addition, labour costs were much lower than those in Hong Kong. Also, as garment industry did not require high technology, lots of garment factories gradually relocated their production line to the Mainland. In those years, many big manufacturers had already set up factories in developing countries in Asia. However, they believed mainland workers were more diligent and intelligent and the differences in wages were insignificant. Together with problems caused by differences in systems and culture, some of the manufacturers considered the investment environment overseas less desirable than that of Mainland China. As a result, they closed the factories overseas and set up factories on the mainland.
The peak to northbound relocation happened at the end of the 1980s thru the early 1990s. Many Hong Kong businessmen chose the nearby Pearl River Delta because of convenient transport and similar languages and cultures. After relocation, the number of workers in these factories doubled. The operational cost was low in China and it facilitated the north-south development of these Hong Kong businesses. On the one hand they expanded textile production in the north, on the other hand they developed retail and built their brands in the south. The local production line was less active after the factories moved north. Apart from managerial staff and skilled workers dispatched to China to guide the production, manufacturers laid off a large number of low-skilled workers, triggering a series of labour litigation regarding severance packages, wages and annual leave.
Many manufacturers still maintained a small production line in Hong Kong after relocating their factories northward in order to take sewed garments from the mainland for post-processing. By doing so they could mark the garment as “Made in Hong Kong” and met the origin requirements of the customers. The model is called Overseas Processing Arrangement (OPA). To deal with the origin spot check from Hong Kong Customs, some manufacturers hired workers to “act” and pretend to be engaged in production. In these twenty years, Hong Kong’s garment production business had more symbolic than actual value as the city had already transformed into a remote control centre for sales, engaging in activities like brand-building, purchasing, logistics and accounting. Twenty years after the relocation to the north, the advantages of setting up factories in the mainland could not be compared to that before. With the minimum wages set up by the government, and the annual rise in social security fees for the workers, labour costs rose sharply. Some Hong Kong businessmen have complained about the increasing difficulty of running garment factories on the mainland. The Hong Kong’s garment industry is facing new challenges.
Reference
1.)Interview with ChanWing Kee, 14 June, 2011.
2.)Interview with Chan Sui Kau, 18 and 25 May, 2011.
3.)Interview with Ah Ying, 7 June 2010.
4.)Interview with Lai Yiu Kai, 4 March, 2010.
5.)Interview with Ha Chong Fong, 17 November 2009.
6.)林根成,「香港製衣工業概況」,《香港棉織業同業公會年刊 1961-1962》,香港: 棉織業同業公會,1962年,頁12。
7.)本會資料室,「製衣工業概況」,《香港布廠商會成立卅七週年紀念特刊》,香港: 香港布廠商會,1977年,頁56-60。
8.)周忠繼,「香港棉系工業之前瞻」,《香港製衣廠商會年刊》,香港: 香港製衣廠商會,1962年,頁21-22。
9.)周文軒,「製衣工業之前途」,《香港製衣廠商會年刊》,香港: 香港製衣廠商會,1962年,頁33-35。
10.)王美,「英國加入共同市場與香港製衣業」,《香港製衣廠商會年刊》,香港: 香港製衣廠商會,1962年,頁37-39。
11.)譚靄然,「當前港製衣業的困難」,《香港製衣廠商會年刊》,香港: 香港製衣廠商會,1962年,頁40。
12.)蔡寶瓊主編,《千針萬線:香港成衣工人口述史》,香港 : 進一步多媒體有限公司,2008年。
13.)工商日報編輯部編輯,《香港華資工廠調查錄》,香港: 工商日報,民國23 (1934年)。
14.)王楚瑩編,《香港工廠調查》,香港: 南僑新聞企業公司,民國36 (1936年)。
Industry Focus
The origins and development of garment industry in Hong Kong
The term “Garment manufacturing” comprises two levels of meanings. It is a process and also an industry. Spinning, weaving, dyeing and sewing are four necessary processes in manufacturing garments. In the early years, the raw materials of garments were cotton textile, therefore “sewing” or “garment manufacturing” was the last process of the cotton-related industry. Many of the large yarn factories in Hong Kong were operated using the “one-stop” production model and garment manufacturing was one of the large departments; at the same time, many garment manufacturing factories did not deal with spinning, weaving or dyeing. They had to rely on local and overseas spinning factories to provide them with knitted fabric. Therefore, garment manufacturing can be regarded as an independent industry. The post-war official industrial statistics addressed the textile industry and the garment industry as two separate entities.
Garment factories can be categorized by products: top (shirt), bottom (trousers), suit, thick and thin garment. Each piece was manufactured in different departments in large-quantity and each worker was responsible for a particular process. The post-war garment factories in Hong Kong were mainly owned by businessmen from Guangdong. Many tailors from Shanghai and Chiuchow also started home-based workshops. Exquisite handicraft like drawnwork, embroidery and Gu embroidery was their selling point, and they offered tailor-made, up-market clothing. Buttons, zippers and printing were peripheral industries attached to garment industry. When talking about Hong Kong garment industry, we refer mainly to garment factories with a flow line production.
The garment industry in Hong Kong took shape in the early twentieth century. At that time there were no independent “garment factories”. The garment department was one of the departments of a weaving mill. Apart from supplying fabrics, many weaving mills produced garments through simple procedures. Factories dedicated to garment manufacturing, and that took names with such words as “Clothing” or “Garment” appeared in the early thirties. Kwong Hing Tai Company, Kwok Man Underwear Company, Kwok Hing Garment Co.,Ltd were some of the large factories found before WWII. Before the war, clothing produced in Hong Kong comprised mainly middle-priced to low-priced products such as vests, cotton knitwear, cotton stretch tee, briefs, cotton-knitted socks, swimsuit etc. They were exported to the Mainland, Nanyang, the Britain Commonwealth and British colonies.
Western clothing became popular around the world after the war. Many Chinese gradually changed their habits and switched from tailor-made Chinese-style clothing to western style shirts and trousers which became a trend. Also, at the end of 1940s many refugees came to Hong Kong and they brought in a large amount of cash, technique and cheap labour, contributing to the prosperity of the garment industry. Post-war garment industry can be briefly classified into four stages: I) Era of exporting to British Colonies (post-war to 1950s); II) Era of exporting to Europe and America (from the end of 1950s); III) Era of setting up factories in poor countries in Asia (from early 1970s); IV) Era of setting up factories in mainland China (from early 1980s). 1970s and 1980s were the golden ages of garment industry. Among all other manufacturing industries, it was the leading industry in terms of number of factories, number of employees and total export value.
The change in product variety and materials
Local garment factories mainly produced underwear before the war. Among them, cotton knitwear, cotton stretch tee and cotton socks were the most popular. In the years right after the war, garment factories produced mainly shirts. In the eye of the general public, garment factories were shirt factories. Shirts made in Hong Kong were mainly mass produced and of mid-to-low pricing. Apart from supplying locally and to the mainland, shirts were also exported to the British colonies such as Malaysia, East Indies, India and Ceylon etc.
Towards the end of 1950s, the opening of the Europe and America market brought the price up for garments exported from Hong Kong, and the variety were more diversified and expanded to trousers, jackets, sleepwear, sportswear etc. Since 1961, the total export value of outfit and trousers had surpassed that of shirts. In the early 1970s, jeans swept through the European and American continents and many local garment factories put them into production. Jeans became the garment with the highest value of total exports of the year. In 1980s, many big garment factories developed their own brands and strengthened the bond between their products with the trend to launch mid-to-high end fashion.
Regarding the methods of knitting the materials, as woven fabric had a longer history, and was produced extensively, it was more suitable for the mass production of mid-to-low price garments. Woven fabrics thus became the mainstream after the war till 1960s. Main garment factories using woven fabrics were Lai Sun Garment, Yangtzekiang Garment and Esquel Garment. Since 1960s, knitted garments became popular. As knitted fabrics could be produced in small-scale and in more styles, its sportswear and casual wear were welcomed by the public. Main knitted garment factories included Laws Garment and Knitting, Fong’s, Unison Knitting and Zentes. Wool knitting is a stream of knitting which flourished in the 1980s and 1990s. Accessories such as shawls were favoured by fashion consumers. Laws Garment and Knitting was an exemplar of the industry this stream.
Before 1960, local garment factories used fabrics mainly from overseas. About seventy per cent of the export garments were processed from imported fabrics; with the prosperity of local textile industry, over fifty percent of the fabrics for export garments were supplied by local factories in the middle of 1970s, especially for denim, khaki and corduroy. Garment factories using local fabrics could lower production costs and raise its competitiveness towards nearby regions.
Production Models: OEM and brand development
Local garment owners had always relied on foreign companies to get in touch with the overseas market. The reason was because they were not familiar with foreign legal systems and culture. Also, the communication channels were not developed. Most garment factories sold their products to foreign companies and these companies directly traded with overseas customers. For example, Dodwell & Co. Ltd. ran business for the British market, and C. Melchers GmbH & Co for the German market, foreign companies owned by Indians operated business for markets from India to African. Garment factories with better finances had another way out. Starting from the end of 1950s, they set up offices in Europe and America, hired local salesmen or cooperated with local agencies so as to get in touch with traditional fashion brands to build the OEM production model.
Since 1960s, OEM had been the core business model of garment industry. American chain-stores like Wal-Mart and K-Mart ordered low-cost garments from Hong Kong garment factories. Local garment factories also produced garments designed by Europe and American brands and supplied them with finished products. For example, Yangtzekiang Garment produced fashion for such brands as Marks & Spencer, Hugo Boss, Marc Jacobs, Nike and Littlewood etc. Such OEM orders were usually stable and large so they were the lifeblood of garment factories; big factories might subcontract part of the order to some middle or small sized factories so as to meet the deadline. These middle or small factories might further split the order to some small-scale factories or even home-style workshops which formed the layers of a sub-contracting web. Such sub-contracting could be by piece, or by a particular process.
Soon after the war Hong Kong garments were exported to the British colonies. Large textile companies and garment factories set up sales department in the Southeast Asia, exported and sold goods directly there. Exported shirts produced in Hong Kong had built their brand in the early years, for example, “The Eagles” by “Kwong Hing Tai” and “The Professor” by Yangtzekiang Garment. However, such catchy brands served only to impress customers and the quality could not be compared to the European and American brands which distinguished themselves by unique designs.
The profit of selling was higher than producing garments. Since 1970s, some garment factory owners started up sales department and some big garment factories started to develop their own brands. They took reference from overseas fashion brands as they created their own brands. For example, Yangtzekiang Garment developed their own brand “Michel Rene” with a French take on the style. They produced and marketed their products. Apart from developing their own brands, garment factory owners also invested in representing certain brands. They brought famous brands from Europe and America, or produced and marketed the brands by themselves, or they collected commission from the retailers. For example, Novel Group had acquired famous U.S. fashion brand Tommy Hilfiger and Chao’s family, founder of the Novel Group, became Hong Kong’s business representative to develop business in the U.S. Apart from promoting foreign brand, there were local garment factories running chain stores for their brands. For example, Bossini was a local brand selling leisurewear in chain stores established in 1987 by the founder of the Laws Group Law Ting Bong.
International market and quota system
Hong Kong’s garment industry has always been directed by export. Before the 1960s, the export market focused on developing countries in which local textile industry was weak. At the same time, Hong Kong was a British colony so it enjoyed the benefits of the preferential tariff treatment offered by countries of the British Commonwealth. It enjoyed privileges when exporting garments to the United Kingdom and the United Kingdom had become one of the main markets for Hong Kong garments; From 1960s, Hong Kong garments were also massively imported to the U.S. market. But since 1950s, many European and American countries had gradually set up trade protection measures to protect their own garment industries. For example, in 1959 Hong Kong had signed an agreement with the United Kingdom to voluntarily restrict the export quantity of cotton textiles; in the International Cotton Textile Meeting held in Geneva in July 1961, a “short-term arrangement” was set on international cotton textile trade to restrict the exporting quantity of twenty-two kinds of Hong Kong textile products. In the early 1970s, the U.S. had officially assigned quotas to Hong Kong cotton textile products and the restriction had later extended from cotton to polyester fibers and chemical fibers.
In 1970s, various kinds of garment products – pure cotton, mix cotton and synthetic fibers etc. were developed. From 1974, Hong Kong had officially named the earlier bilateral trade agreement set with EU and the U.S. as “Multi-fiber Agreement”. The agreement had systematically assigned codes to various textiles and the restriction was initially for cotton, synthetic fibers and wool, but in 1986 it had extended to ninety percent of textile products exported to the U.S. The agreement explained how the quota system should be implemented: the importing and exporting counties may negotiate quota restrictions based on recent exporting situation and set the exporting quantity and variety, then with reference to the quantity of garment production in various factories quotas were assigned.
Garment industry was the biggest industry in Hong Kong. The Hong Kong Government had great concerns about how the quota had influenced the industry. In 1970s and 1980s, it sent various delegations to participate in international trade conferences and negotiated with EU and the U.S. on the quota issue of textile products. This series of quota negotiations on textile products were governed under the “General Agreement on Tariff and Trade” (GATT) conference organizations. Hong Kong government sent the Deputy Director of Trade and Industry Department as chief representative of negotiation, and Textile Advisory Board (TAB) members attended so as to give immediate advice. TAB members were appointed by the government and were from the industrial sector and the business sector. The Hong Kong delegation played a leading role among the Asian countries. In those years, many Hong Kong businessmen set up factories in Southeast Asia and they were active in their local textile industries. They also participated as representatives of those countries and negotiated on the quota in the meetings. In those international meetings, members from Hong Kong garment industry represented different countries to negotiate on quota restrictions.
All these quotas and product origin restrictions had profound influences on the garment industry. Quotas were assigned according to the quantity of production so large factories or factories with a long history hold more quotas. Some factories resold the quotas to factories with no or insufficient quotas to obtain profits; small factories with no quotas could only took over the outsourced orders from big factories and relied on big factories to survive; some factories rearranged their production, such as raised the quantity of high priced garments and the products unrestricted to export. Many big factories built factories in countries unrestricted by the quotas. Closer ones were Macau and Taiwan, and further ones were Southeast Asia, South Asia and Africa, and directly from there they exported the products to developed countries like Europe and the U.S.
As Hong Kong was a British colony, many Hong Kong businessmen took British colonies as their first choice for investment. Singapore, Malaysia, Myanmar, Sri Lanka and Bangladesh were top choices. They obtained overseas investment information mainly through organizations like the Hong Kong Trade Development Council, British banks and KPMG etc. To set up factories in less developed countries, Hong Kong businessmen enjoyed the benefits of cheap land and labour, and in turn supported the local textile industry so it was welcome by the local governments. Of course they had to tackle operational problems brought by cultural differences.
Factories, workers and production techniques
Before the war, cotton textile factories dominated the garment industry and were located in districts such as Sham Shui Po, Mongkok, Yau Ma Tei and Kowloon City etc; there were a few garment factories scattered in Central & Western District and Kowloon City. In the early years after the war, garment industry prospered and factories mainly gathered in Sham Shui Po and Cheung Sha Wan. There were many factories producing textiles and clothes around so the supply of raw materials was abundant. A “through-train” interactive relationship was formed among the factories. Big companies usually built one whole building as their factory, smaller ones rented a floor. There were also even smaller informal or home-style workshop scattered around Hong Kong. In the early 1960s, the Hong Kong government developed industrial districts like Kwun Tong and San Po Kong. As the land use was restricted as industrial the price was cheaper so it attracted many factory owners to buy the land and build the factories; at the same time the government built industrial buildings and rented them to smaller factories. The government also built resettlement buildings next to them so as to provide labour to the factory owners.
Garment industry was labour-intensive. The garment factories were of smaller scale before the war. A factory with dozens of workers would be regarded as big. The industry developed rapidly thirty years after the war. Workers in the garment industry accounted for fifteen percent of labour during the peak. Big factories could easily employ thousands of workers. The larger the garment factory, the more sophisticated the division of labour in production. Division of labour was assigned according to types of garments and processes of sewing. The more sophisticated the division, the lower the skills required. The division is less sophisticated in smaller factories yet the skills required were higher.
The male and female ratio in garment industry was about thirty to seventy. There was a clear gender division of labour. Male were usually skilled workers or technicians and they monopolized cutting and ironing. Female were usually manual or unskilled workers mainly responsible for sewing and packing etc. After working in big factories for a few years, some masters of cutting started up small or informal factories to take outsourced orders from their former employees or from other big factories. Factory workers were usually paid by piece so it helped to raise motivation while at the same time lower the factory’s production costs.
In the 1970s and 1980s, the industry was booming to such scales that manufacturers were too busy to attend to all orders during the peak seasons. They outsourced their orders to informal or home-style workshops. During those years, many married women who had worked in factories started up sewing workshops at home, or rented a place at resettlement buildings or at the public housing so as to take orders from big factories. The outsourced work helped these women balance work and family. At the same time, it allowed manufacturers to retain a flexible production team. Home-based workers with better craftsmanship could be assigned to make samples and earned more per piece.
Swift to the north and restructuring of the industry
In the early 1980s, Hong Kong’s land and wages were raising rapidly. Like other labour-intensive industry such as watches, toys and electronics, garment industry faced pressure from the increasing operational costs. The opening and reform allowed China to actively introduce investments from over the border and encourage Hong Kong businessmen to set up factories there. Privileges on tax and land price were offered; in addition, labour costs were much lower than those in Hong Kong. Also, as garment industry did not require high technology, lots of garment factories gradually relocated their production line to the Mainland. In those years, many big manufacturers had already set up factories in developing countries in Asia. However, they believed mainland workers were more diligent and intelligent and the differences in wages were insignificant. Together with problems caused by differences in systems and culture, some of the manufacturers considered the investment environment overseas less desirable than that of Mainland China. As a result, they closed the factories overseas and set up factories on the mainland.
The peak to northbound relocation happened at the end of the 1980s thru the early 1990s. Many Hong Kong businessmen chose the nearby Pearl River Delta because of convenient transport and similar languages and cultures. After relocation, the number of workers in these factories doubled. The operational cost was low in China and it facilitated the north-south development of these Hong Kong businesses. On the one hand they expanded textile production in the north, on the other hand they developed retail and built their brands in the south. The local production line was less active after the factories moved north. Apart from managerial staff and skilled workers dispatched to China to guide the production, manufacturers laid off a large number of low-skilled workers, triggering a series of labour litigation regarding severance packages, wages and annual leave.
Many manufacturers still maintained a small production line in Hong Kong after relocating their factories northward in order to take sewed garments from the mainland for post-processing. By doing so they could mark the garment as “Made in Hong Kong” and met the origin requirements of the customers. The model is called Overseas Processing Arrangement (OPA). To deal with the origin spot check from Hong Kong Customs, some manufacturers hired workers to “act” and pretend to be engaged in production. In these twenty years, Hong Kong’s garment production business had more symbolic than actual value as the city had already transformed into a remote control centre for sales, engaging in activities like brand-building, purchasing, logistics and accounting. Twenty years after the relocation to the north, the advantages of setting up factories in the mainland could not be compared to that before. With the minimum wages set up by the government, and the annual rise in social security fees for the workers, labour costs rose sharply. Some Hong Kong businessmen have complained about the increasing difficulty of running garment factories on the mainland. The Hong Kong’s garment industry is facing new challenges.
Reference
1.)Interview with ChanWing Kee, 14 June, 2011.
2.)Interview with Chan Sui Kau, 18 and 25 May, 2011.
3.)Interview with Ah Ying, 7 June 2010.
4.)Interview with Lai Yiu Kai, 4 March, 2010.
5.)Interview with Ha Chong Fong, 17 November 2009.
6.)林根成,「香港製衣工業概況」,《香港棉織業同業公會年刊 1961-1962》,香港: 棉織業同業公會,1962年,頁12。
7.)本會資料室,「製衣工業概況」,《香港布廠商會成立卅七週年紀念特刊》,香港: 香港布廠商會,1977年,頁56-60。
8.)周忠繼,「香港棉系工業之前瞻」,《香港製衣廠商會年刊》,香港: 香港製衣廠商會,1962年,頁21-22。
9.)周文軒,「製衣工業之前途」,《香港製衣廠商會年刊》,香港: 香港製衣廠商會,1962年,頁33-35。
10.)王美,「英國加入共同市場與香港製衣業」,《香港製衣廠商會年刊》,香港: 香港製衣廠商會,1962年,頁37-39。
11.)譚靄然,「當前港製衣業的困難」,《香港製衣廠商會年刊》,香港: 香港製衣廠商會,1962年,頁40。
12.)蔡寶瓊主編,《千針萬線:香港成衣工人口述史》,香港 : 進一步多媒體有限公司,2008年。
13.)工商日報編輯部編輯,《香港華資工廠調查錄》,香港: 工商日報,民國23 (1934年)。
14.)王楚瑩編,《香港工廠調查》,香港: 南僑新聞企業公司,民國36 (1936年)。

