RECENTLY VISITED
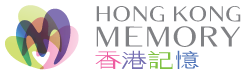
Industry Focus
The origins of the Hong Kong metal industry
Metal has been used as an industrial raw material since the ancient times. The more commonly used metals include gold, silver, copper, iron and tin. Due to advancement in technology in the twentieth century, new metals and alloys are extensively utilized in which stainless steel is more prominent. Metal products come in great varieties – as small as screws, pins, nails and watchcases, or as large as tableware and kitchenware, toys and auto parts. They cover a variety of military and civilian goods. Methods to manufacturing them include casting, stamping, lathing and so on.
By nature, metal industry can be divided into metal smelting, products manufacturing and parts & components production. Smelting is a heavy industry. It requires significant capital and technology investment in such processes as copper casting, iron casting and steel production. Smelting industry also includes metal cutting and shaping. Iron and steel plants provide raw materials to manufacturing factories. Metal products factories produce different types of metal consumer goods, examples of which include flashlight factories and kitchenware factories which specialize in individual products. There also exist integrated factories that manage a number of metal goods. Parts & components factories are mainly subsidiaries of manufacturing factories. They produce metal parts for toys, watches and household goods.
Various types of local metal factories form a pyramid structure. At the top are a few steel plants, producing copper, iron, steel and other raw materials. They form the industrial upstream. Various kinds of metal products factories represent the pyramid body. Their products are supplied both to local and foreign markets. They are the backbone of the industry. The bottom of the pyramid consists of a large number of small parts factories. These factories are scattered everywhere and they are the foundation of the metal industry. In addition to the regular metal factory, there are molding, planting, polishing and other factories, which are responsible for all specialized processes.
Metal industry of Hong Kong started budding in the 1920s. Many entrepreneurs from Guangzhou came to set up factories in Hong Kong. Before WWII most manufacturers of the metal industry were of medium scale, producing flashlight, batteries, thermos and enamel products, which were exported to the Mainland, Southeast Asia and the Commonwealth regions. In the early years, metal factories gathered in Tai Kok Tsui, Sham Shui Po, Mong Kok and Sai Ying Pun, etc. These areas were the fringes of the urban area at the time. Because of the lower price of the land, factories usually occupied single-block buildings.
The emergence of post-war steel-making industry
The emergence of steel-making industry was a major breakthrough for the post-war metal industry of Hong Kong. The birth of steel plants was stemmed from the ship dismantling industry. After WWII there were a large number of shipwrecks in Hong Kong waters, including warships sunk during wartime. They were a rich source of scrap metal. From post-war to the early 1960s, the ship dismantling industry developed prosperously. More than 200 ship-dismantling companies and several thousand workers made a living by collecting scrap metal at the peak. Large amounts of local scrap metal were exported to Japan.
The demobilization period saw an explosion of development in all areas of society. The population explosion triggered the housing boom, coupled with the rise of industries, led to a high demand in steel bars, copper, iron and other metals. Many businessmen invested in the salvaging and dismantling of ships. Some of them sold the harvested scrap metals while some other businessmen set up steel plants using this opportunity. Chiaphua Components and Shiu Wing Steel Ltd. were leaders in the local steel industry; investment in ship dismantling provided an opportunity for them to thrive.
Steel-forging is one of a few local heavy industries. Steel plants occupy a large piece of land; factories are equipped with furnaces, rolling mills and other heavy equipment. Production processes include melting, casting, molding and welding. The technologies required are more advanced than that of metal factories. As Steel plants require sea water for cooling so they are generally built on the seaside. For example, Chiaphua was located at To Kwa Wan and Shiu Wing was set up at Tiu Keng Leng. Some steel plants not only produced iron bars, steel bars and other semi-manufactured goods for local industrial and construction purposes, but also produced consumer goods, constituting a vertical production model. They became the elite enterprises in the metal industry. With the emergence of steel plants, local factories were less dependent on foreign raw materials. However, since the conditions to develop heavy industry were lacking in Hong Kong, more than half of the raw materials still needed to be imported from the United Kingdom, the United States, Japan and other countries. Manufacturers were inevitably affected by the fluctuations in raw material pricing.
The rise of metal parts factories
Along with the boom of electronics, watches and toy industries in the 1960s and the 1970s, there was a thirst for metal parts and components. A large number of metal parts factories sprung up. They produced tiny products such as watchcases, radio screws, pot handles and other pieces of kitchen utensils. Founders of many metal parts factories were skilled workers from the manufacturing factories. They started their factories with very limited funding. At that time, large-sized manufacturing factories were generally reluctant to invest in producing metal parts. They mainly co-operated with metal parts factories by outsourcing orders to them.
The majority of metal parts factories were domestic-scale workshops. They were found all over Hong Kong. Some of them were in Chinese-style old tenements or ground floor shops while some were set up in industrial buildings. Only a few electric die-cutting machines, lathe, planer and some other simple machines were found in the workshops. They were usually supplied by local machine factories. Number of workers for each workshop was usually below twenty. Many of them were family members and a small number of apprentices were recruited. Small-scale manufacturers did not join associations. They only had tea gatherings to exchange information with peers on a regular basis, so their knowledge to the industry operation was rather limited. They were often strongly affected by economic crisis. For instance, during the world oil crisis at the end of 1974, domestic export of radios dropped sharply, which led to the closure of many radio parts factories.
The trend of domestic workshops changed the ecosystem of the industry, with the number of metal factories raising substantially. The number of factories increased by more than tenfold from 1950 to 1970 and peaked at 6000 factories in 1980. At the same time, the size of factories shrank gradually, dropping from 50 people per factory in the 1950s to less than 10 people per factory in the 1980s. Small metal parts factories became the mainstream of the metal industry. However, some parts factories had more potential of development, such as those produced key watchcase parts. Some manufacturers managed to grow out of the domestic workshop operation model after starting their business for more than ten years. They were able to contact foreign clients directly, or set up factories with foreign companies.
Industrialists, masters and workers
Metal products factories and parts factories utilize many large machines, such as lathe, planer, milling machines for metal cutting and shaping. Creating the mould, furbishing, electroplating and other support processes require craftsmanship. So founders of many metal factories either had a technical background, or had worked as master craftsmen in other factories, or had received tertiary education. There was a strong culture of entrepreneurship in the metal industry. Many founders started their business in their twenties and thirties with meager savings to become a small factory owner.
Apprenticeship was common in metal factories. This was the case for both large factories and domestic parts workshops, but the benefits and training methods of apprentices were different. Domestic workshops emphasized on mentoring relationships. Master and apprentice were like father and son. The apprenticeship ritual involves the apprentice serving tea on their knees; apprentices were also responsible for caring for the master’s daily living. Domestic workshops provided harsh training for apprentices. Apprentices were required to serve their apprenticeship for three years. Apprentices had to do odd jobs in the first half of their apprenticeship with their master or the factories to support their living. Since apprentices had not mastered the crafts in the early stage and wasted lots of materials, apprentices had to stay in the factory for a year or two after finishing their apprenticeship to make money for the factory. Apprentices of large metal factories had better benefits. Factories also provided food and accommodation. Apprentices did not need to serve the apprenticeship for three years. Masters were employed by the manufacturers, so they were also employees of the factories. Apprentices did not have to serve them as elders.
Metal factories required more manual labour, involving the use of heavy machinery, and workers had to carry heavy copper and iron. Also, with the foul air and deafening noise, the metal industry employed more male workers compared to garment, electronics, watches and other industries. Masters and apprentices of metal factories were mostly male. Females were responsible for packing and other simple processes. Male workers were better treated and permanently employed, and offered food and accommodation. Female workers were generally temporary workers, with salaries paid on a daily basis. In the early years, a strong human touch could be found in metal factories. Manufacturers attached importance to family and hometown ties, so they preferred to hire relatives and fellow
townsmen. Even if they suffered losses for many years, they would still choose keep the business open to avoid affecting their employee’s livelihood.
Evolution of metal products
Only consumer goods were produced in Hong Kong before the war. The post-war metal industry tended to be more developed. There were steel plants producing steel in the upstream, and domestic workshops producing metal parts in the downstream. Both large metal products and small metalware were manufactured, forming a one-stop model of operation. Metal products underwent a major evolution over the past decades. Flashlights made in Hong Kong were leading products before the war. Battery and light bulb factories were attached to flashlight factories. After the Sino-Japanese War broke out, large numbers of military products such as helmets and masks were supplied to the market. Flashlights were no longer in need and gradually died out as the war ended. Military products also lost its foothold in the market. Kitchenware, enamelware, toys and commodities became mainstream products after the war. Along with the rise of toys, watches and electronics industry, various types of metal parts became available.
Local businessmen who were engaged in raw materials trading organized a trade guild in 1930, named the “Hong Kong Copper and Iron Merchants Association”. This name reflected that the major materials used in products in those days were copper and iron. Raw material industry developed rapidly after the war, and new metals were continuously developed. Various types of alloys were successfully researched and developed. Materials for metal products also became diversified. The first aluminum plant in Hong Kong was founded in 1953. The aluminum industry had already hired more than 700 workers after several years, and 80% of the products were exported. The first stainless steel plant was founded in 1959. In the 1960s, stainless steel was widely used in the production of kitchenware.
In addition to improvement of product types and materials, techniques had significantly improved after the war. High-tech metal products accounted for a higher proportion. With the advancement in stamping technology, factories that specialized in bronze ware were able to handle harder stainless steel, so these factories were able to evolve to manufacturing stainless steel utensils. Besides, Round zinc-carbon batteries dominated the battery industry for a long period. Layer built batteries and micro-cells were successively introduced in the 1960s and 1970s, and they were applied to high-tech electronic products. Moreover, plastic emerged rapidly as a raw material in the post-war period, which provided manufacturers with new material combinations. Many mixed type metal products had emerged after the war. For example, the Freezinhot brand of hot water bottles that mixed metal, plastic and glass.
The operation model of metal factories
Domestic metal products were mainly for export. Because of cultural ties and tariff preferences, South East Asia and the Commonwealth countries were the chief markets before the war. In the 1970s, the United States became the largest market and the United Kingdom relegated to the second place. After the open door and reform policy were implemented in China, many metal factory owners turned their focus to the Mainland. In 1988, China replaced the U.S. and became the largest export market of Hong Kong metal industry. This trend has continued ever since. Relative to watches, electronics, toys, garment and other mainstream industries, metal industry had a higher proportion of local sales. Among them, “Sam Yuen” and “Freezinhot” were famous local brands. Some manufacturers took part in the Hong Kong Products Expo to promote the company image as well as their products.
The OEM model appeared early in metal industry, especially for torches, batteries and similar products. These two were the early industries in Hong Kong, and up until 1950s, many torch and batteries factories had been in business for more than twenty years. As they possessed mature production technology and quality control, these enterprises were well-known overseas. In those years, many veteran U.S. manufacturers had ceased local production and switched over to giving OEM orders to Hong Kong manufacturers and forming partnerships. Hong Kong factories produced according to the specifications for the U.S. companies. Well-known partnerships included Chiaphua Industries Limited---Ray O Vac, Hing Wah Battery---Winchester and Nam Jam Factory---Ever Ready etc.
As some OEM customers had specific and stringent requirements, the standards of quality control of the finished goods varied. OEM customers could also place orders with other manufacturers which would reduce the profits of individual factories. In addition, large OEM orders might not be an advantage to the manufacturers as it would occupy a high percentage of the factory’s production capacity, giving the market too much control over the model of operation. Therefore, for high-tech manufacturers, OEM was not a mainstream model. They tended to use ODM and OBM models, and designed products according to the manufacturer’s market sense or market research. They marketed their products to customers. At the same time they built their own brands to strengthen the competitiveness in the retail market so as to strive for higher profit for the enterprise.
Metal factories established right after WWII were mainly of a smaller scale. The manufactures paid more attention to the affairs related to production and they did not have much knowledge for the customers and the market. They only took reference from popular goods from overseas, improved on them and relied on the trading companies for the orders and sales. In the late 1960s, many factories expanded rapidly and their ability to take orders and sales improved. Therefore, these companies would either directly dealt with overseas customers or would set up agency companies overseas to make arrangements for OEM and ODM businesses. The role of the rading companies became secondary.
Production relocation and business transformation
Production relocation in the metal industry started as early as the 1960s. A small number of factory owners began to start up plants in Southeast Asia and Taiwan to utilize the cheap land and labor, and to free themselves from the protectionist restrictions. These regions were just at the beginning stage of industrialization. Hong Kong businessmen setting up factories there could facilitate technology transfer but they also had to face a lot of problems caused by cultural difference. Large-scale production relocation began in the early 1980s. In the 1970s, the government strengthened health and fire regulations, and metal factories that were less profitable suffered the brunt of the impact. Coupled by rising labor and land costs, and competition from industrialization in the neighboring regions, local metal business became more difficult. Traditional industries like the battery industry were most severely affected.
The open door and reform policy on the Mainland in the late 1970s encouraged foreign investment. The low production cost attracted a large number of metal factories to move north and set up factories in the nearby Pearl River Delta in the 1980s. In the early stages, Hong Kong businessmen implemented compensation trade and processing on order. As Hong Kong’s future and the political situation of China became optimistic, strong companies expanded their investment in the early 1990s. They built their own large-scale factories based on the “three accesses and one lot” fashion (it is a saying referring to good access to water, electricity and transport, plus a land lot for building factories). They dedicated additional effort into promoting their brands and domestic sales and made China their main production base with a focus on the China market. After setting up factories in China, the production lines in Hong Kong shrank gradually. The factories in Hong Kong were repurposed into offices for processing orders, accounts and logistics. They were switching from a manufacturing to a services mode of operation.
Metal industry in Hong Kong goes back a long way in time. Many big factories were set up before the war and were handed to the second generation in the 1960s and the 1970s. The second generation of owners had received western education and mastered knowledge in professional business management and production. After taking over, the power of family-style management faded out. At the same time, manufacturers pursued diversification in products and business. They recruited highly educated talents and gradually transformed traditional family business to modern enterprises.
Reference
1.)Interview with Sun Kin Chao and Mrs. Sun, 28 March 2011.
2.)Interview with Sun Kai Lit, 28 March 2011.
3.)Interview with Yu Lap Ming, Yu Tat Ching and Ms. Yu, 13 December 2010.
4.)Interview with Lo Lei Wo, 16 November and 23 November 2010.
5.)Interview with Leung Wai Ho, 21 August, 28 August and 18 September.
6.)‘For Dining or Display---Gleaming Bronze Cutlery’, Hong Kong Trade Bulletin, Hong Kong: Dept. of Commerce and Industry (May1957), p.145-147.
7.)‘Shining Success---Aluminum-ware is a Leading Export’, Hong Kong Trade Bulletin, Hong Kong: Dept. of Commerce and Indusry (August 1957), p.272-273. 8.)‘Manufacture of Torch Cases and Bulbs’, Hong Kong Trade Bulletin, Hong Kong: Dept. of Commerce and Industry (March 1959), p.63-65.
9.)‘Grace at Meals’, Hong Kong Trade Bulletin, Hong Kong: Dept. of Commerce and Industry (April 1962), p.158-160.
10.)Lee Chi-wing Helen, Metalware industry in Hong Kong, Undergraduate essay presented in the Dept. of Geography & Geology, University of Hong Kong, 1966.
11.)Pong Ping Kwun, A comparative survey of three light industries in Hong Kong: battery, electronics and optics, Undergraduate essay presented in the Dept. of Geography & Geology, University of Hong Kong, 1966.
12.)麥錦燦,「五金業前途的展望」,《香港五金商業總會自置會所紀念刋》(香港: 香港五金商業總會,1953年),頁90-91。
13.)陸乃瑤,「年來五金業之展望」,《香港五金商業總會自置會所紀念刋》(香港: 香港五金商業總會,1953年),頁92-93。
14.)曾樹屏,「舊五金---『廢鐵』在五金市場所佔的地位」,《香港五金商業總會卅週年紀念特刊》(香港: 香港五金商業總會,1960年),頁53-54。
15.)曾樹屏,「『一九五七年』香港五金市價的波動所予後人的教訓」,《香港五金商業總會卅週年紀念特刊》(香港: 香港五金商業總會,1960年),頁57-58。
16.)江文,「十年來五金市場的變化 為本會三十週年紀念而作」,《香港五金商業總會卅週年紀念特刊》(香港: 香港五金商業總會,1960年),頁59。
17.)工業署資料及聯絡事務部編,「第十章 金屬製品業」,《一九九〇年香港製造業》(香港:工業署,1990年),頁151-165。
Industry Focus
The origins of the Hong Kong metal industry
Metal has been used as an industrial raw material since the ancient times. The more commonly used metals include gold, silver, copper, iron and tin. Due to advancement in technology in the twentieth century, new metals and alloys are extensively utilized in which stainless steel is more prominent. Metal products come in great varieties – as small as screws, pins, nails and watchcases, or as large as tableware and kitchenware, toys and auto parts. They cover a variety of military and civilian goods. Methods to manufacturing them include casting, stamping, lathing and so on.
By nature, metal industry can be divided into metal smelting, products manufacturing and parts & components production. Smelting is a heavy industry. It requires significant capital and technology investment in such processes as copper casting, iron casting and steel production. Smelting industry also includes metal cutting and shaping. Iron and steel plants provide raw materials to manufacturing factories. Metal products factories produce different types of metal consumer goods, examples of which include flashlight factories and kitchenware factories which specialize in individual products. There also exist integrated factories that manage a number of metal goods. Parts & components factories are mainly subsidiaries of manufacturing factories. They produce metal parts for toys, watches and household goods.
Various types of local metal factories form a pyramid structure. At the top are a few steel plants, producing copper, iron, steel and other raw materials. They form the industrial upstream. Various kinds of metal products factories represent the pyramid body. Their products are supplied both to local and foreign markets. They are the backbone of the industry. The bottom of the pyramid consists of a large number of small parts factories. These factories are scattered everywhere and they are the foundation of the metal industry. In addition to the regular metal factory, there are molding, planting, polishing and other factories, which are responsible for all specialized processes.
Metal industry of Hong Kong started budding in the 1920s. Many entrepreneurs from Guangzhou came to set up factories in Hong Kong. Before WWII most manufacturers of the metal industry were of medium scale, producing flashlight, batteries, thermos and enamel products, which were exported to the Mainland, Southeast Asia and the Commonwealth regions. In the early years, metal factories gathered in Tai Kok Tsui, Sham Shui Po, Mong Kok and Sai Ying Pun, etc. These areas were the fringes of the urban area at the time. Because of the lower price of the land, factories usually occupied single-block buildings.
The emergence of post-war steel-making industry
The emergence of steel-making industry was a major breakthrough for the post-war metal industry of Hong Kong. The birth of steel plants was stemmed from the ship dismantling industry. After WWII there were a large number of shipwrecks in Hong Kong waters, including warships sunk during wartime. They were a rich source of scrap metal. From post-war to the early 1960s, the ship dismantling industry developed prosperously. More than 200 ship-dismantling companies and several thousand workers made a living by collecting scrap metal at the peak. Large amounts of local scrap metal were exported to Japan.
The demobilization period saw an explosion of development in all areas of society. The population explosion triggered the housing boom, coupled with the rise of industries, led to a high demand in steel bars, copper, iron and other metals. Many businessmen invested in the salvaging and dismantling of ships. Some of them sold the harvested scrap metals while some other businessmen set up steel plants using this opportunity. Chiaphua Components and Shiu Wing Steel Ltd. were leaders in the local steel industry; investment in ship dismantling provided an opportunity for them to thrive.
Steel-forging is one of a few local heavy industries. Steel plants occupy a large piece of land; factories are equipped with furnaces, rolling mills and other heavy equipment. Production processes include melting, casting, molding and welding. The technologies required are more advanced than that of metal factories. As Steel plants require sea water for cooling so they are generally built on the seaside. For example, Chiaphua was located at To Kwa Wan and Shiu Wing was set up at Tiu Keng Leng. Some steel plants not only produced iron bars, steel bars and other semi-manufactured goods for local industrial and construction purposes, but also produced consumer goods, constituting a vertical production model. They became the elite enterprises in the metal industry. With the emergence of steel plants, local factories were less dependent on foreign raw materials. However, since the conditions to develop heavy industry were lacking in Hong Kong, more than half of the raw materials still needed to be imported from the United Kingdom, the United States, Japan and other countries. Manufacturers were inevitably affected by the fluctuations in raw material pricing.
The rise of metal parts factories
Along with the boom of electronics, watches and toy industries in the 1960s and the 1970s, there was a thirst for metal parts and components. A large number of metal parts factories sprung up. They produced tiny products such as watchcases, radio screws, pot handles and other pieces of kitchen utensils. Founders of many metal parts factories were skilled workers from the manufacturing factories. They started their factories with very limited funding. At that time, large-sized manufacturing factories were generally reluctant to invest in producing metal parts. They mainly co-operated with metal parts factories by outsourcing orders to them.
The majority of metal parts factories were domestic-scale workshops. They were found all over Hong Kong. Some of them were in Chinese-style old tenements or ground floor shops while some were set up in industrial buildings. Only a few electric die-cutting machines, lathe, planer and some other simple machines were found in the workshops. They were usually supplied by local machine factories. Number of workers for each workshop was usually below twenty. Many of them were family members and a small number of apprentices were recruited. Small-scale manufacturers did not join associations. They only had tea gatherings to exchange information with peers on a regular basis, so their knowledge to the industry operation was rather limited. They were often strongly affected by economic crisis. For instance, during the world oil crisis at the end of 1974, domestic export of radios dropped sharply, which led to the closure of many radio parts factories.
The trend of domestic workshops changed the ecosystem of the industry, with the number of metal factories raising substantially. The number of factories increased by more than tenfold from 1950 to 1970 and peaked at 6000 factories in 1980. At the same time, the size of factories shrank gradually, dropping from 50 people per factory in the 1950s to less than 10 people per factory in the 1980s. Small metal parts factories became the mainstream of the metal industry. However, some parts factories had more potential of development, such as those produced key watchcase parts. Some manufacturers managed to grow out of the domestic workshop operation model after starting their business for more than ten years. They were able to contact foreign clients directly, or set up factories with foreign companies.
Industrialists, masters and workers
Metal products factories and parts factories utilize many large machines, such as lathe, planer, milling machines for metal cutting and shaping. Creating the mould, furbishing, electroplating and other support processes require craftsmanship. So founders of many metal factories either had a technical background, or had worked as master craftsmen in other factories, or had received tertiary education. There was a strong culture of entrepreneurship in the metal industry. Many founders started their business in their twenties and thirties with meager savings to become a small factory owner.
Apprenticeship was common in metal factories. This was the case for both large factories and domestic parts workshops, but the benefits and training methods of apprentices were different. Domestic workshops emphasized on mentoring relationships. Master and apprentice were like father and son. The apprenticeship ritual involves the apprentice serving tea on their knees; apprentices were also responsible for caring for the master’s daily living. Domestic workshops provided harsh training for apprentices. Apprentices were required to serve their apprenticeship for three years. Apprentices had to do odd jobs in the first half of their apprenticeship with their master or the factories to support their living. Since apprentices had not mastered the crafts in the early stage and wasted lots of materials, apprentices had to stay in the factory for a year or two after finishing their apprenticeship to make money for the factory. Apprentices of large metal factories had better benefits. Factories also provided food and accommodation. Apprentices did not need to serve the apprenticeship for three years. Masters were employed by the manufacturers, so they were also employees of the factories. Apprentices did not have to serve them as elders.
Metal factories required more manual labour, involving the use of heavy machinery, and workers had to carry heavy copper and iron. Also, with the foul air and deafening noise, the metal industry employed more male workers compared to garment, electronics, watches and other industries. Masters and apprentices of metal factories were mostly male. Females were responsible for packing and other simple processes. Male workers were better treated and permanently employed, and offered food and accommodation. Female workers were generally temporary workers, with salaries paid on a daily basis. In the early years, a strong human touch could be found in metal factories. Manufacturers attached importance to family and hometown ties, so they preferred to hire relatives and fellow
townsmen. Even if they suffered losses for many years, they would still choose keep the business open to avoid affecting their employee’s livelihood.
Evolution of metal products
Only consumer goods were produced in Hong Kong before the war. The post-war metal industry tended to be more developed. There were steel plants producing steel in the upstream, and domestic workshops producing metal parts in the downstream. Both large metal products and small metalware were manufactured, forming a one-stop model of operation. Metal products underwent a major evolution over the past decades. Flashlights made in Hong Kong were leading products before the war. Battery and light bulb factories were attached to flashlight factories. After the Sino-Japanese War broke out, large numbers of military products such as helmets and masks were supplied to the market. Flashlights were no longer in need and gradually died out as the war ended. Military products also lost its foothold in the market. Kitchenware, enamelware, toys and commodities became mainstream products after the war. Along with the rise of toys, watches and electronics industry, various types of metal parts became available.
Local businessmen who were engaged in raw materials trading organized a trade guild in 1930, named the “Hong Kong Copper and Iron Merchants Association”. This name reflected that the major materials used in products in those days were copper and iron. Raw material industry developed rapidly after the war, and new metals were continuously developed. Various types of alloys were successfully researched and developed. Materials for metal products also became diversified. The first aluminum plant in Hong Kong was founded in 1953. The aluminum industry had already hired more than 700 workers after several years, and 80% of the products were exported. The first stainless steel plant was founded in 1959. In the 1960s, stainless steel was widely used in the production of kitchenware.
In addition to improvement of product types and materials, techniques had significantly improved after the war. High-tech metal products accounted for a higher proportion. With the advancement in stamping technology, factories that specialized in bronze ware were able to handle harder stainless steel, so these factories were able to evolve to manufacturing stainless steel utensils. Besides, Round zinc-carbon batteries dominated the battery industry for a long period. Layer built batteries and micro-cells were successively introduced in the 1960s and 1970s, and they were applied to high-tech electronic products. Moreover, plastic emerged rapidly as a raw material in the post-war period, which provided manufacturers with new material combinations. Many mixed type metal products had emerged after the war. For example, the Freezinhot brand of hot water bottles that mixed metal, plastic and glass.
The operation model of metal factories
Domestic metal products were mainly for export. Because of cultural ties and tariff preferences, South East Asia and the Commonwealth countries were the chief markets before the war. In the 1970s, the United States became the largest market and the United Kingdom relegated to the second place. After the open door and reform policy were implemented in China, many metal factory owners turned their focus to the Mainland. In 1988, China replaced the U.S. and became the largest export market of Hong Kong metal industry. This trend has continued ever since. Relative to watches, electronics, toys, garment and other mainstream industries, metal industry had a higher proportion of local sales. Among them, “Sam Yuen” and “Freezinhot” were famous local brands. Some manufacturers took part in the Hong Kong Products Expo to promote the company image as well as their products.
The OEM model appeared early in metal industry, especially for torches, batteries and similar products. These two were the early industries in Hong Kong, and up until 1950s, many torch and batteries factories had been in business for more than twenty years. As they possessed mature production technology and quality control, these enterprises were well-known overseas. In those years, many veteran U.S. manufacturers had ceased local production and switched over to giving OEM orders to Hong Kong manufacturers and forming partnerships. Hong Kong factories produced according to the specifications for the U.S. companies. Well-known partnerships included Chiaphua Industries Limited---Ray O Vac, Hing Wah Battery---Winchester and Nam Jam Factory---Ever Ready etc.
As some OEM customers had specific and stringent requirements, the standards of quality control of the finished goods varied. OEM customers could also place orders with other manufacturers which would reduce the profits of individual factories. In addition, large OEM orders might not be an advantage to the manufacturers as it would occupy a high percentage of the factory’s production capacity, giving the market too much control over the model of operation. Therefore, for high-tech manufacturers, OEM was not a mainstream model. They tended to use ODM and OBM models, and designed products according to the manufacturer’s market sense or market research. They marketed their products to customers. At the same time they built their own brands to strengthen the competitiveness in the retail market so as to strive for higher profit for the enterprise.
Metal factories established right after WWII were mainly of a smaller scale. The manufactures paid more attention to the affairs related to production and they did not have much knowledge for the customers and the market. They only took reference from popular goods from overseas, improved on them and relied on the trading companies for the orders and sales. In the late 1960s, many factories expanded rapidly and their ability to take orders and sales improved. Therefore, these companies would either directly dealt with overseas customers or would set up agency companies overseas to make arrangements for OEM and ODM businesses. The role of the rading companies became secondary.
Production relocation and business transformation
Production relocation in the metal industry started as early as the 1960s. A small number of factory owners began to start up plants in Southeast Asia and Taiwan to utilize the cheap land and labor, and to free themselves from the protectionist restrictions. These regions were just at the beginning stage of industrialization. Hong Kong businessmen setting up factories there could facilitate technology transfer but they also had to face a lot of problems caused by cultural difference. Large-scale production relocation began in the early 1980s. In the 1970s, the government strengthened health and fire regulations, and metal factories that were less profitable suffered the brunt of the impact. Coupled by rising labor and land costs, and competition from industrialization in the neighboring regions, local metal business became more difficult. Traditional industries like the battery industry were most severely affected.
The open door and reform policy on the Mainland in the late 1970s encouraged foreign investment. The low production cost attracted a large number of metal factories to move north and set up factories in the nearby Pearl River Delta in the 1980s. In the early stages, Hong Kong businessmen implemented compensation trade and processing on order. As Hong Kong’s future and the political situation of China became optimistic, strong companies expanded their investment in the early 1990s. They built their own large-scale factories based on the “three accesses and one lot” fashion (it is a saying referring to good access to water, electricity and transport, plus a land lot for building factories). They dedicated additional effort into promoting their brands and domestic sales and made China their main production base with a focus on the China market. After setting up factories in China, the production lines in Hong Kong shrank gradually. The factories in Hong Kong were repurposed into offices for processing orders, accounts and logistics. They were switching from a manufacturing to a services mode of operation.
Metal industry in Hong Kong goes back a long way in time. Many big factories were set up before the war and were handed to the second generation in the 1960s and the 1970s. The second generation of owners had received western education and mastered knowledge in professional business management and production. After taking over, the power of family-style management faded out. At the same time, manufacturers pursued diversification in products and business. They recruited highly educated talents and gradually transformed traditional family business to modern enterprises.
Reference
1.)Interview with Sun Kin Chao and Mrs. Sun, 28 March 2011.
2.)Interview with Sun Kai Lit, 28 March 2011.
3.)Interview with Yu Lap Ming, Yu Tat Ching and Ms. Yu, 13 December 2010.
4.)Interview with Lo Lei Wo, 16 November and 23 November 2010.
5.)Interview with Leung Wai Ho, 21 August, 28 August and 18 September.
6.)‘For Dining or Display---Gleaming Bronze Cutlery’, Hong Kong Trade Bulletin, Hong Kong: Dept. of Commerce and Industry (May1957), p.145-147.
7.)‘Shining Success---Aluminum-ware is a Leading Export’, Hong Kong Trade Bulletin, Hong Kong: Dept. of Commerce and Indusry (August 1957), p.272-273. 8.)‘Manufacture of Torch Cases and Bulbs’, Hong Kong Trade Bulletin, Hong Kong: Dept. of Commerce and Industry (March 1959), p.63-65.
9.)‘Grace at Meals’, Hong Kong Trade Bulletin, Hong Kong: Dept. of Commerce and Industry (April 1962), p.158-160.
10.)Lee Chi-wing Helen, Metalware industry in Hong Kong, Undergraduate essay presented in the Dept. of Geography & Geology, University of Hong Kong, 1966.
11.)Pong Ping Kwun, A comparative survey of three light industries in Hong Kong: battery, electronics and optics, Undergraduate essay presented in the Dept. of Geography & Geology, University of Hong Kong, 1966.
12.)麥錦燦,「五金業前途的展望」,《香港五金商業總會自置會所紀念刋》(香港: 香港五金商業總會,1953年),頁90-91。
13.)陸乃瑤,「年來五金業之展望」,《香港五金商業總會自置會所紀念刋》(香港: 香港五金商業總會,1953年),頁92-93。
14.)曾樹屏,「舊五金---『廢鐵』在五金市場所佔的地位」,《香港五金商業總會卅週年紀念特刊》(香港: 香港五金商業總會,1960年),頁53-54。
15.)曾樹屏,「『一九五七年』香港五金市價的波動所予後人的教訓」,《香港五金商業總會卅週年紀念特刊》(香港: 香港五金商業總會,1960年),頁57-58。
16.)江文,「十年來五金市場的變化 為本會三十週年紀念而作」,《香港五金商業總會卅週年紀念特刊》(香港: 香港五金商業總會,1960年),頁59。
17.)工業署資料及聯絡事務部編,「第十章 金屬製品業」,《一九九〇年香港製造業》(香港:工業署,1990年),頁151-165。

